Hello Human,
In Steelmaking: Part 1, we learned about the role of steel in our and how we currently make it.
We also learned that steelmaking emits 2.6 Gt of direct CO2 emissions annually and accounts for 8% of the global final energy demand. Slashing the steel industry’s emissions- and energy intensity is crucial in tackling the climate crisis.
In this Part 2, we’ll look at three routes to producing low-emission steel. Get ready for some awesome science!
If you haven’t read Part 1 of this deep dive series yet, I highly recommend doing so before continuing reading.
Let’s make some low-emissions steel!
➡️Follow Survivaltech.club on Twitter and Linkedin💚
🗞️Updates
📊Survivaltech.club’s resource database. I started collecting exciting hardware climate startups in this database. My plan is to expand this database to include (deep tech) climate investors, grants, and other useful resources for founders, scientists, investors, and climate people. In the meantime, check out more resources here on Survivaltech.club’s website.
🎙️Interview about Carbon Removal. Maki.vc, a European VC firm, asked me to share my insights on carbon removal in their latest Sunday newsletter! Read it here.
🦅Bird’s-eye view into decarbonizing steel production
There are three key routes to the steel industry’s decarbonization:
Decarbonize primary production
Decarbonize secondary production
Increase the share of secondary production
Note: If you find yourself confused with the steelmaking jargon (primary production, electric arc furnaces, etc.), I recommend checking out Part 1 of this steelmaking deep dive series.
🧪1. Decarbonize primary production: novel technologies
Decarbonizing steel’s primary production is tricky.
In the Blast Furnace-Blast Oxygen Furnace (BF-BOF) route, which makes 70% of our steel today, coal is an integral part of the process. Coal turns into carbon monoxide, which then acts as the chemical agent separating metallic iron and oxygen from the iron ore.
There are three ways to achieve limited CO2 reductions in primary production 1) BF-BOF process optimization, 2) Bioenergy, e.g. biocoke, and 3) Carbon Capture, Utilization, and Storage (CCUS). While these measures play a role in lowering the steel industry’s emissions in the short term, we cannot rely solely on them.
Luckily, there are three radical CO2 reduction technologies for steel’s primary production:
Hydrogen-based direct reduction
Hydrogen plasma
Electrolysis
This kind of revolutionary stuff excites me, so let’s go through these technologies individually.
1. Hydrogen-based direct reduction
In hydrogen-based direct reduction, natural gas is replaced by hydrogen in the direct reduction process. Hydrogen acts as a chemical agent separating metallic iron and oxygen from iron ore.
Hydrogen can be produced from water and renewable electricity via electrolysis. (Read more about green hydrogen in Survivaltech.club’s deep dive on green hydrogen).
Below is a short overview of the hydrogen-based direct reduction process at the HYBRIT project by SSAB, LKAB, and Vattenfall.
The clear advantage of hydrogen-based direct reduction is that natural gas in the direct reduction process can be partly or even fully replaced with hydrogen relatively easily. This reduces capital costs. Natural gas-based direct reduction is already commercially used, making up 5% of the global steel production.
If you read an announcement about a new “green steel plant”, the new plant is going to use hydrogen-based direct reduction with high probability. (Check out announced projects here.)
A disadvantage of the hydrogen-based direct reduction is its requirement of high iron content. The insufficient iron ore supply with high iron content may become a serious bottleneck.
Companies:
H2 Green Steel, Sweden
GreenIron, Sweden
2. Hydrogen plasma
The hydrogen plasma-based steelmaking process produces crude steel from iron ore in one single step.
In hydrogen-based direct reduction, the resulting sponge iron must still be processed in an EAF before it becomes crude steel. Using hydrogen plasma reduces these steps to one single step. The iron oxide gets reduced and melted at the same time.
Here’s an excellent explanation of the steelmaking process with hydrogen plasma.
The advantages of the hydrogen plasma process include lower capital cost and energy demand. Read more details about hydrogen plasma’s advantages in this research paper.
However, the hydrogen plasma process is still a novel technology and requires substantial development before it is scaled and its climate impact gets realized.
Companies:
Ferrum Decarb, Germany
SuSteel by Voestalpine, Austria
3. Electrolysis
Electrolysis is an electrochemical process that can be applied to steelmaking in addition to making green hydrogen.
In electrolysis, the iron metal is extracted from the iron oxide by passing an electric current through electrodes. The process also needs an appropriate electrolyte.
Below is a video where Boston Metal explains how they make steel with the Molten Oxide Electrolysis process. Here’s an even better video explaining the extraction of metals from oxides via electrolysis. (Isn’t electrolysis cool!)
The disadvantage of the Molten Oxide Electrolysis process is that it requires a high temperature (1600°C / 2900 F). The iron oxide needs to be melted, as the name implies. Luckily, there’s a research project called Σiderwin developing low-temperature electrolysis for steelmaking. Here’s a great explanation of Σiderwin’s method.
Like hydrogen plasma-based steelmaking, electrolysis is a novel technology in steelmaking and requires substantial development before realizing its potential climate impact.
Companies:
Boston Metal, USA
Σiderwin (research project), Spain
⚡2. Decarbonize secondary production: switch to renewable electricity
Decarbonizing the secondary production is much more straightforward than decarbonizing the primary production.
Secondary production uses an electric arc furnace (EAF) to melt the steel scrap and produce new steel. As the EAF’s name implies, it uses electricity as the energy source. The electricity can be easily switched to renewable energy.
♻️3. Increase the share of secondary production
Increasing the share of secondary production (=recycled steel) makes sense, even if all electricity could not immediately be supplied from renewable energy sources in secondary production,
Producing steel from scarp in an EAF (secondary production) is much less energy- and emissions-intensive than making steel from iron ore via the Blast Furnace-Blast Oxygen Furnace (BF-BOF) and Direct Reduction Iron - EAF (DRI-EAF) route (primary production).
Secondary production uses a lot less energy to start with. According to IEA, the scrap-based EF uses 2.1 GJ to produce one ton of steel, while BF-BOF and natural gas-based DRI-EAF use a staggering 21.4 GJ / t and 17.1 GJ/t, respectively.
The BF-BOF process, which makes 70% of our steel today, uses a whopping 10x more energy than the scrap-EAF route.
The Scrap-EAF route is commercially viable, producing 25% of our steel today. Hence, its technology risk is low and is ready to be scaled.
The caveat in increasing the rate of steel recycling is that there is currently not enough high-quality scrap steel available to meet the demand.
Steel recycling suffers especially from copper contamination. Scarp steel contains copper from, e.g., copper wires and motors. Too much copper in recycled steel causes surface cracks and limits the applications of recycled steel to low-quality applications, such as reinforcement bars.
There’s currently no commercial way to remove copper from steel scrap. Here’s a paper of solutions that could be scaled.
💚Reason to stay positive
The steel industry has adopted fast novel technologies over the decades once better alternatives have become available. I would have never guessed this!
This historical trend gives a reason for optimism that even such a bulky industry as steelmaking can decarbonize once we bring novel technologies out from the lab to the market.
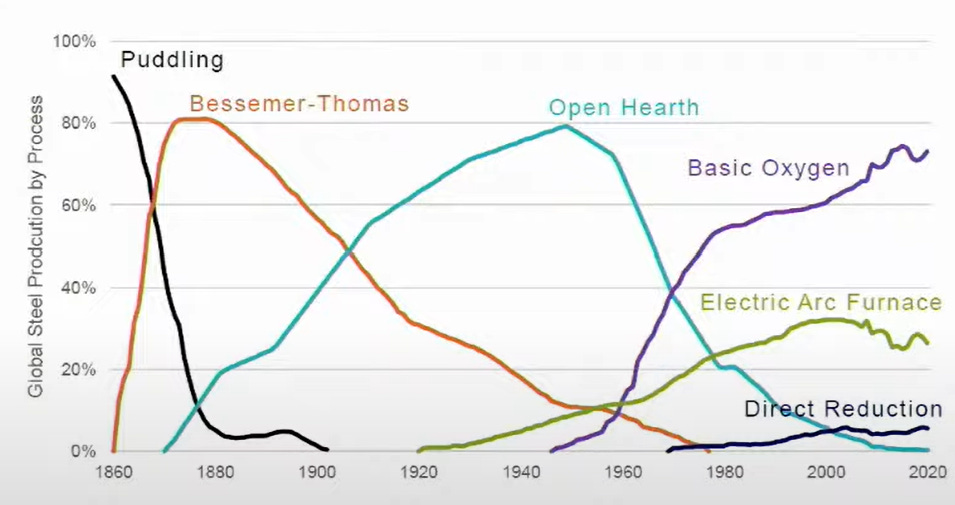
Further reading
LeadIT’s database of green steel projects. (This is awesome!)
Thank you, Michael Campos from Azolla Ventures, and Andreas Weber from Ferrum Decarb, for sharing your insights on decarbonizing steelmaking with me!
As always, I’d love to hear feedback and connect with fellow climate people! Contact me at pauliina@survivaltech.club, Twitter, or LinkedIn.
If you found this article useful, please share it with your network!🌍
➡️Follow Survivaltech.club on Twitter and Linkedin
Best, Pauliina💚
Sources
AtlanticCouncil (2022). EnergySource Innovation Stream with Boston Metal: Decarbonizing the steel industry. Link.
Bill Gates (2019). Better Metal. Link.
Daehn, K. E., Serrenho, A. C. & Allwood, J. M. (2017). How Will Copper Contamination Constrain Future Global Steel Recycling? Environmental Science & Technology, 51(11), 6599-6606. Link.
Daehn, K. E., Serrenho, A. C. & Allwood, J. M. (2019). Finding the Most Efficient Way to Remove Residual Copper from Steel Scrap. Metallurgical and Materials Transactions B, 50, 1225-1240. Link.
Fan Z. & Friedmann, S. J. (2021). Low-carbon production of iron and steel: Technology options, economic assessment, and policy. Joule, 5(4), pp. 829-862. Link.
IEA (2020), Iron and Steel Technology Roadmap, IEA, Paris. Link.
McKinsey (2020). Decarbonization challenge for steel. Link.
Nicholas, S. & Basirat, S. (2022). Iron ore quality a potential headwind to green steelmaking. IEEFA. Link.
Sabat, K. C. & Murphy. A. B. (2017). Hydrogen Plasma Processing of Iron Ore. Metallurgical and Materials Transactions B, 48, 1561-1594. Link.
Vattenfall (2017). Fossil free steel production: This is HYBRIT. Link.