Interview with Lilian Schwich, CEO & Co-Founder of cylib #56
Efficient and climate-friendly battery recycling
Hello Human,
I am excited to share this interview with the amazing Lilian Schwich, CEO and Co-Founder of cylib!
Cylib is an Aachen-based startup developing an efficient and climate-friendly battery recycling process. They raised a €8M seed round led by World Fund earlier this year and are building the first pilot facility now.
➡️Follow Survivaltech.club on Twitter and Linkedin
🗞️Updates
I was selected for the inaugural US DOE-funded Cradle to Commerce climate technology commercialization program! Our team is focused on high-temperature process heat decarbonization. We conduct customer discovery across manufacturing industries (e.g., cement, glass, steel, non-ferrous metals) and would highly appreciate introductions. Message me here💚
Steady Energy, a small nuclear reactor startup, raised a €2M seed round. Steady Energy is a spinout from VTT, the Finnish state-backed research institution. Love this!
🔋The battery challenge
EVs are rolling onto the streets. The IEA estimates that 50% of the global car stock will be electric by 2040.
As lithium-ion batteries have a lifetime of 15-20 years, lots of batteries will have to be recycled or repurposed for other less demanding applications like stationary energy storage. To be precise, there is expected to be 1300GWh of end-of-life batteries by 2040.
Battery recycling is necessary to prevent batteries from ending up in landfills and environmental hazards from occurring. Battery recycling can also reduce the material demand for primary metals (metals processed from ores). The ICCT estimates that implementing battery recycling can decrease the material demand for new EV batteries by as much as 28% in 2050!
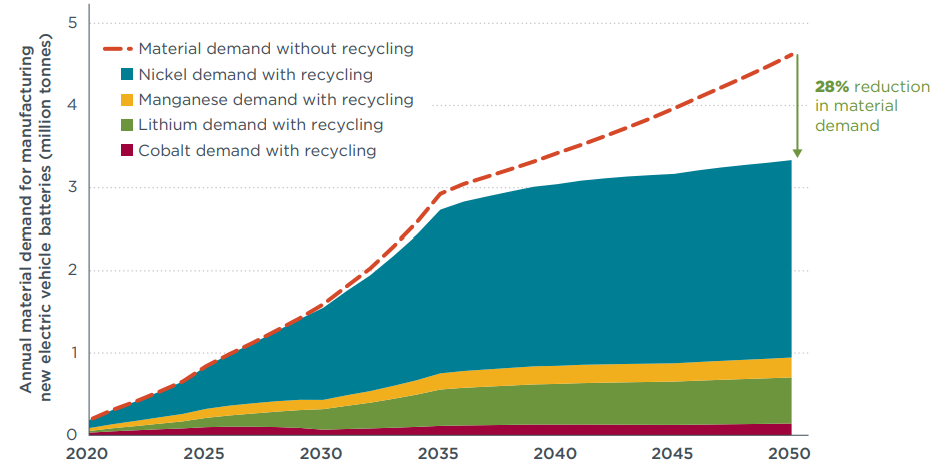
♻️cylib’s solution
cylib is an Aachen-based deeptech startup developing an environmentally friendly end-to-end battery recycling process.
🧠Wisdom from Lilian
What’s the founding story of cylib?
We are a deeptech company originating from RWTH Aachen University, Germany. Both my co-founder Paul Sabarny and I studied and did research there. While I studied materials engineering, Paul’s focus was on minerals engineering.
My curriculum in materials engineering included metallurgy, which studies how metals containing mineral ores are turned into final products. Metallurgy is a fascinating topic! However, it also taught me how big the carbon and environmental footprint of metals and mining are. Mining destroys the environment in several ways, and metal processing is energy- and carbon-intensive. This made me consider recycling end-of-life metal products and side products coming from metallurgical streams from metal production.
Paul was doing his Master’s at RWTH and had a growing interest in EV and micro-mobility battery recycling. As I was the only person at the time researching battery recycling at our university, he reached out to me. I was a Ph.D. student at the time, and Paul wrote his master’s thesis with me on battery recycling. That’s how we got to know each other.
Together, we also did technical consulting at our professor’s spin-off company. We talked with major chemical companies and automotive OEMs that often asked us about how battery recycling works and how they could do it. We realized that the big companies did not have as mature recycling processes as we had thought. Furthermore, we noticed that there were flaws in the current battery recycling processes.
What challenges do the current battery recycling solutions have?
The current battery recycling methods recover only part of the battery materials. Typically, only the most valuable elements of the battery meaning cobalt, nickel, and partly copper are recycled from batteries. These elements make up only 20% of the whole battery pack in terms of their weight.
But in a cathode, there are more elements, especially lithium and manganese, and besides, a lithium-ion battery has not only a cathode’s active materials, but also aluminum casings, copper and aluminum foil, and an anode. The cathode usually contains lithium and transition metal oxides like cobalt. There is a variety of options for anode materials, but typically graphite is used.
The fact that only 20% of the battery materials are recovered is a problem from the environmental perspective but increasingly so from the legislative viewpoint. A new law will become in force soon in the EU that also demands lithium recovery from batteries. [More about that later in this article.]
Another challenge in battery recycling specific to Europe is that most battery materials from end-of-life EV batteries are shipped overseas after initial processing in Europe. Most European battery recyclers disassemble the battery packs and shred them producing something called the “black mass”. The black mass contains valuable active cathode materials and anode materials. The black mass is then shipped to countries like Canada, where the black mass is processed into battery raw materials by environmentally critical methods with poor recovery rates.
The European battery recycling sector is capable of only treating 370,000 tons of end-of-life batteries per year. Of those 370,000 tons of batteries, around 75% is processed only until black mass and not to battery raw materials. As the EU has limited mining activity, it should limit the amount of critical minerals it ships away.
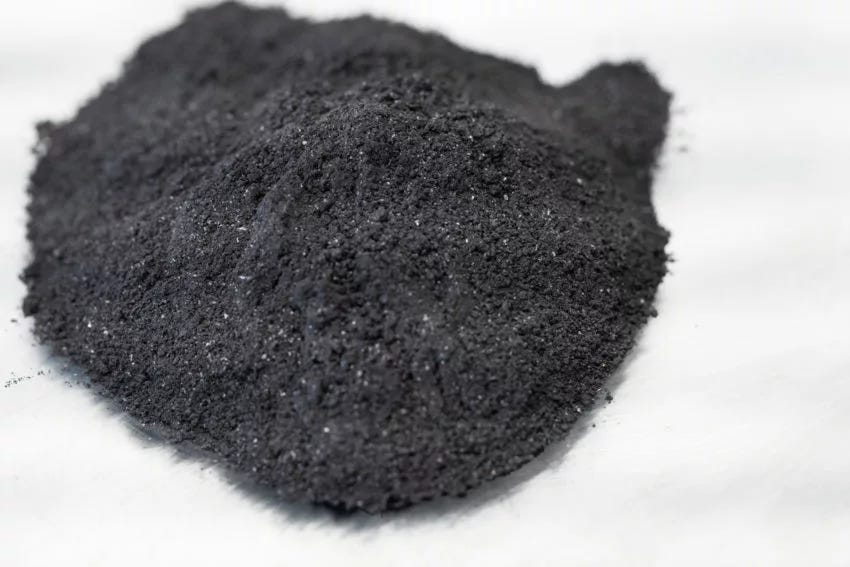
How is cylib tackling this?
cylib has a unique end-to-end process, which recycles lithium-ion batteries into raw materials in a more climate-friendly way. Our battery recycling process consists of mechanical and thermal treatments and also of hydrometallurgy.
When developing our cylib process, we focused on recovering most elements of the lithium-ion battery in a cost-efficient way. Unlike most battery recycling processes, the cylib process also recovers lithium and graphite, reaching 90% overall recycling efficiency.
In our processes’ hydrometallurgy step, we use cleaner hydrometallurgy to recover lithium and graphite. The recovery of lithium is water-based and free from strong acids and additives. Graphite is also recovered via a water-based process. This is possible because we developed a unique pre-treatment and all together, making us unique in the whole world.
The more chemicals or additives like sodium carbonate are used in the process, the higher the embedded carbon footprint of the process is. Manufacturing these chemicals requires energy and produces emissions. Furthermore, high-additive and chemical processes tend to be less environmentally friendly.
How do you source your end-of-life batteries? Who owns the battery, and how do you expect the battery ownership structure to change?
Automotive OEMs for instance are a highly important future client on the supply side, but also cell producers or TIER 1 companies. We are also excited to collaborate as we see the most significant increase in battery volume taking place in the mobility sector. The mobility sector will supply 2 million tons of end-of-life batteries annually from 2040 onwards - only in the EU. We are currently discussing with OEMs about different collaboration options.
There are two likely ways in which the end-of-life battery collection and taking out batteries from a vehicle will take place. One scenario is that the car producers will collect the batteries, take batteries out of the EVs in their own dismantling centers, and then directly charge a recycler. The other scenario is that the OEMs will commission intermediate traders to collect and distribute the batteries to the recycler. While both scenarios are probable, we think it makes sense to aim for direct collaboration with an OEM.
How is the EU legislation on battery recycling now, and how do you think it will change?
We are still relying on the EU’s Battery Directive from the year 2006. This directive provided a good start for the battery recycling industry, as it demands a 50% recycling rate (also known as recycling efficiency) based on the cell level.
There is room for improvement in the 2006/66/EC Battery Directive. The legislation does not require the recovery of all elements, such as lithium and graphite. In addition, the legislation holds a narrow view of recycled elements as it sets cell-level recycling targets. EV battery packs consist of not only battery cells, but also pack and module casings and pack electronics, which should all be recycled. For example, pack and module casings are made from aluminum, an energy-intensive metal.
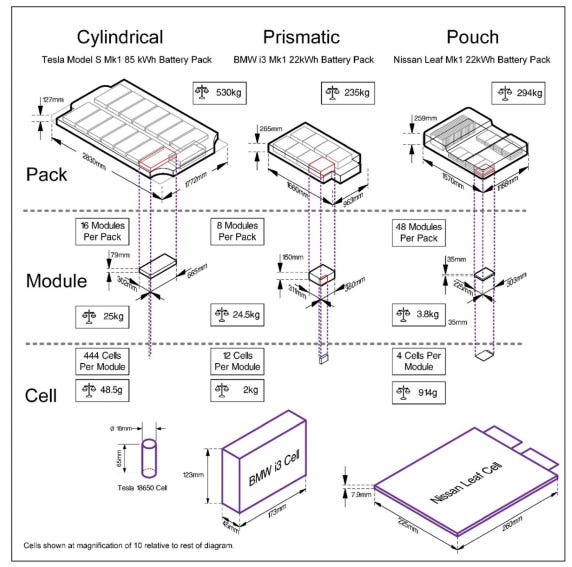
Luckily, a new law on battery recycling is entering into force in the EU soon. On Wednesday, June 14, 2023, the European Parliament approved new rules for the design, production, and waste management of all types of batteries sold in the EU. The new law sets stricter recovery targets for copper, cobalt, and nickel, and introduces recovery targets for lithium. It also poses stricter collection rates for portable and micro-mobility batteries.
The recovery rate targets are, however, still unfortunately missing graphite. This is surprising as the EU considers graphite as a critical mineral. Also, some sort of punishment if the set targets are not reached, is lacking. The punishment for not reaching the set targets will most likely be implemented on the national level but will take several years.
You are building a pilot facility. Congrats! Could you tell more about that the pilot line?
Our pilot factory is a huge step for us, and we are very excited about it! We are building it here in Aachen, Germany, which has several strategic benefits. Aachen is well-located near the borders of the Netherlands and Belgium and in the federal county of North Rhine Westphalia, where there is a tradition in different industry sectors. The nearby RWTH University gives us access to lots of excellent technical talent.
Our goal is to treat EV battery packs, modules, and cells as well as micro-mobility batteries in our pilot factory. The pilot line will be able to treat one battery pack (300-500kg) per day and will handle the whole end-of-end process. We are aiming for building a full-scale industrial line soon, in which we can replicate and scale up this pilot line.
How can the Survivaltech.club readers be helpful to you?
We are hiring! We are looking to strengthen the sales and chemical engineering side of our team. We are also looking for people who have experience in building large-scale industrial operations, especially in the area of hydrometallurgy and process technology. These skills come in handy when building our first industrial pilot line.
While we are well-financed by amazing deeptech and climate tech investors, we will be raising Series A soon. I’m always happy to chat with potential investors in advance!
🌍The Drop - Malmö, Sweden - September 7
The Drop, a one-of-a-kind EU-funded climate tech conference, is back for its second year on September 7th, 2023, in Malmö, Sweden. I attended The Drop in 2022 and absolutely loved it!
➡️Apply for a ticket for a chance to participate and make unexpected connections, have your mind changed by fresh takes on climate solutions, and meet the people who could change the trajectory of your climate career.
I’d love to hear feedback and connect with fellow climate people! Contact me at pauliina@survivaltech.club, Twitter, or LinkedIn.
If you enjoyed this article, please share it with your network!🌍
➡️Follow Survivaltech.club on Twitter and Linkedin
Best, Pauliina💚